What is Process Mapping and How to Get Started
Are you experiencing process problems? Do you regularly see bottlenecks? Lost paperwork? Processes that take too much time?
Process Mapping is a critical step to conduct prior to implementing a process solution as it'll help you address the underlying problems rather than masking them with technology.
What is Process Mapping?
Process mapping is the visual representation of the flow of work where participants visualize the steps in a process. Institutions and businesses typically implement process mapping as part of continuous improvement initiatives. Process mapping helps to identify strengths and weaknesses in a process and improve efficiency and productivity.
Lean Six Sigma is a common system employed in a continuous improvement initiative. Lean Six Sigma is a time-tested approach to increase efficiency.
When you embark on your Lean Six Sigma journey, you’ll need to choose which type of process map to build. There are many different methods for process mapping, each with their own pros and cons. Here are three examples: SIPOC, high level process map, and swimlane map.
SIPOC: SIPOC is an acronym for supplier, inputs, process, outputs, customer. This process map identifies what the process accomplishes and its key players, in very simple terms. It can be very beneficial in explaining the process to others and defining project scope.
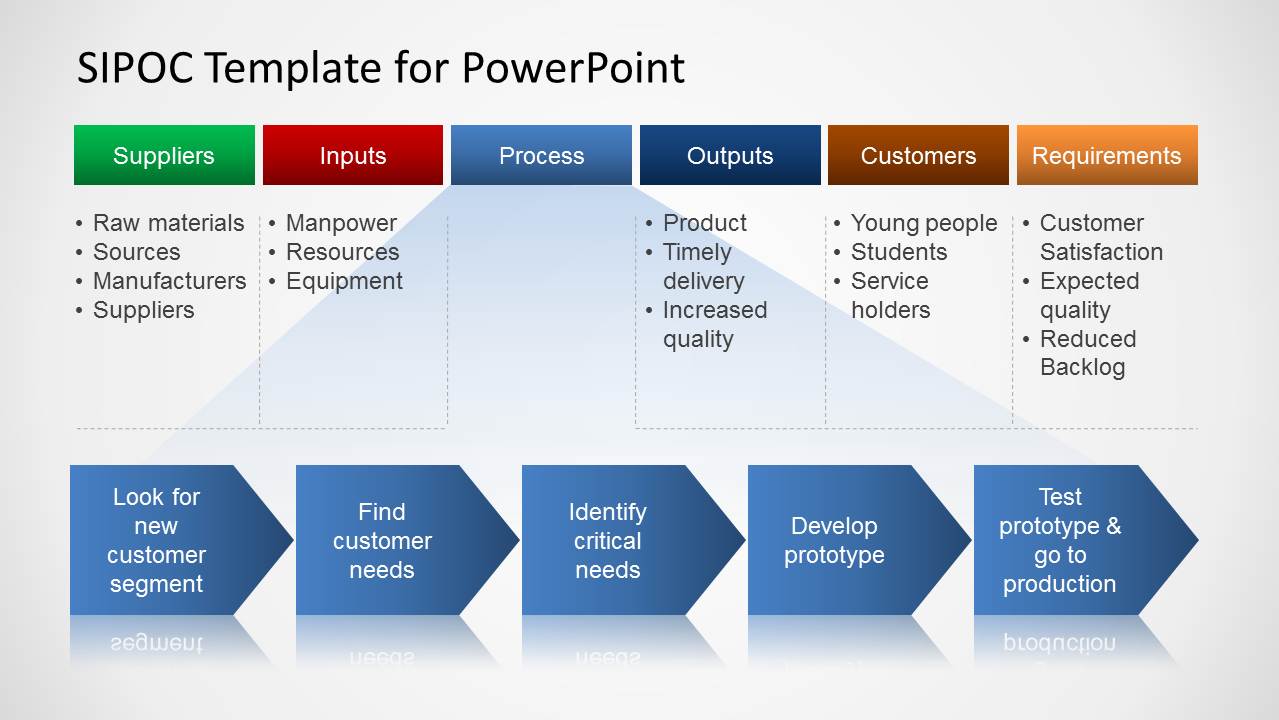
High Level Process Map: Think of the high level process map as a view of the process from 5,000 feet. The purpose is to show what the process does without getting into the minutiae of how it is accomplished. It’s useful when communicating with leaders who don’t need to know all of the details. Of course, it isn’t useful to understand every single step of the process; for that objective, the detailed process map methodology would be a better approach.
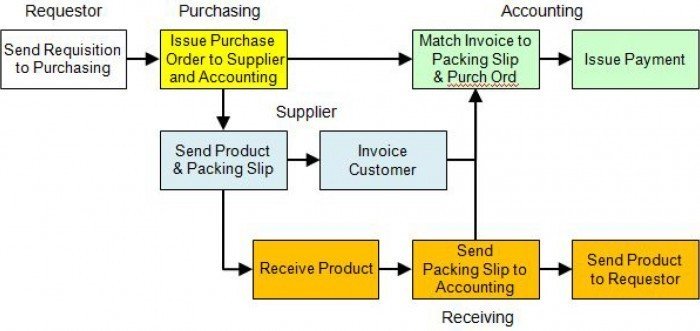
Swimlane Map: The swimlane map places all of the steps into lanes by who accomplishes them. This map is effective in showing who does what. Handoffs are clearly shown through arrows that cross lanes. However, this map can be confusing when used for a process with many steps. Dozens of arrows crossing lanes can cause more confusion. Additionally, this method is not the most space-efficient. One lane, such as a C-level leader, might be almost empty while other lanes have dozens of steps.
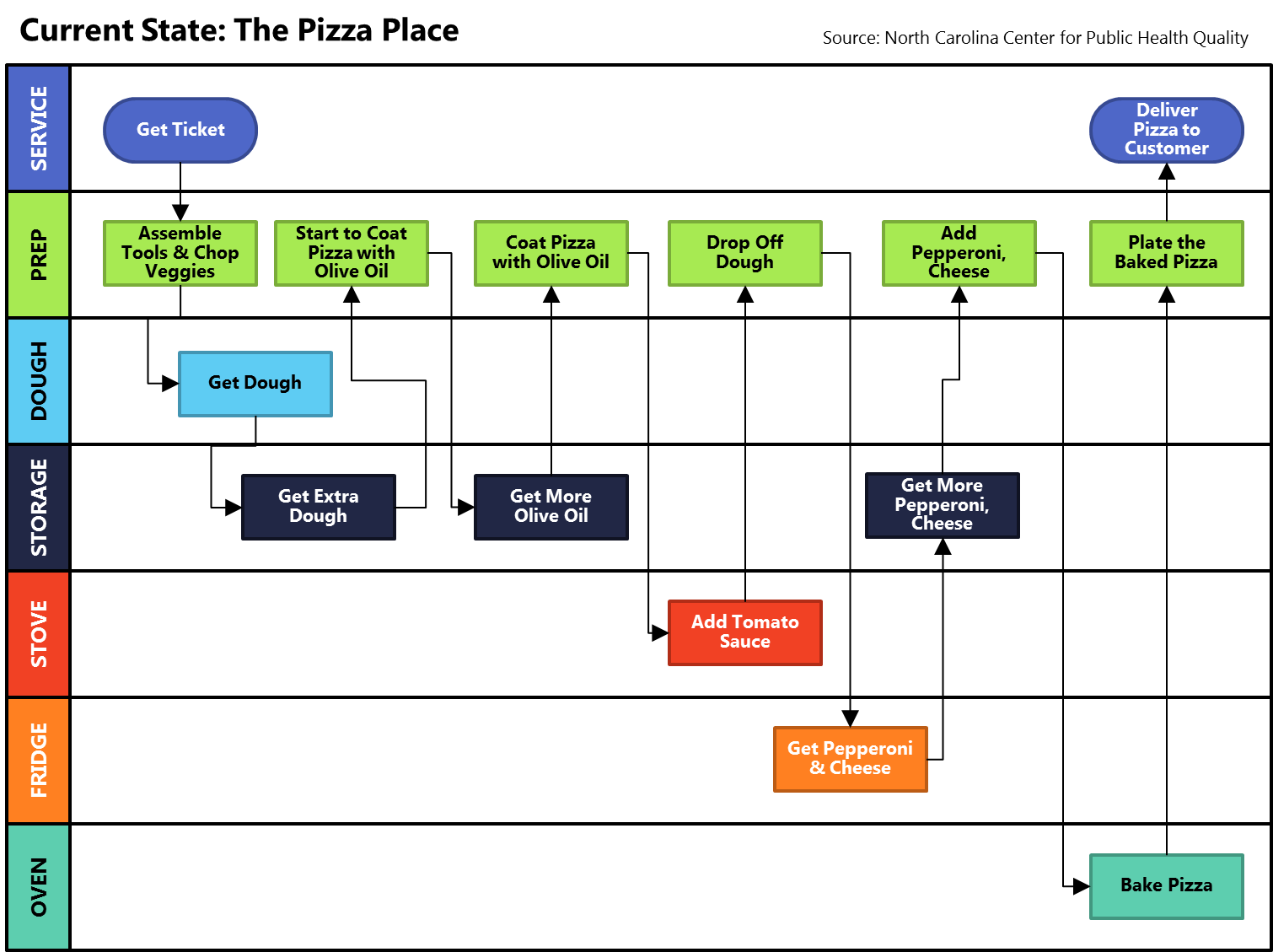
You can find three more examples of process map methodologies here.
Why do Institutions Need Process Mapping?
Process mapping is a means to achieve improved efficiency. By mapping the process out, you can understand it and brainstorm ways to iterate. You might be surprised to find duplication of work, or workarounds previously put in place that have become obsolete.
Benefits of process mapping
- See the whole process in one place. Seeing the process will help you take abstract ideas and make them tangible.
- Identify waste. See repetition, workarounds, and opportunities for streamlining.
- Improve communication. Process mapping helps each player understand their role in the whole process.
- Documentation for future training. After completing a process mapping discussion, store the visual representation of the process in its final state to use as a resource during onboarding.
When is it useful?
Improving efficiency and productivity is never a bad thing, but process mapping can be particularly useful in cross-department processes. Your department might have 10+ processes that go through payroll. Have you ever connected with that office to see if there’s a better way to complete the process?
How to Get Started
1. Select a process. You may want to consult with others and select a process that needs improvement, but won’t be too difficult to tackle.
2. Involve others. As you begin to work through processes, it is essential to bring others to the table. With additional minds involved, the end result will likely be more creative and successful than working on the problem alone. You could hold a process mapping session, virtually if need be, to test process mapping with a group.
3. Pick your process map methodology and build the process. All you need is a pen and sticky notes, or the back of a napkin to create your masterpiece J.K Rowling style.
You can even find a digital process mapping tool to share with your peers if you’re working remotely, or have limited time in the office. Zen Flowcharts is a great tool that we’ve used, and you can try the service for free.
4. Brainstorm better ways to complete the process. Start by seeking out bottlenecks and discussing how you can dismantle them. A process management tool with built-in reporting makes it easy to identify problematic steps within a process. It may be beneficial to interview additional process stakeholders. Are they getting what they need? Do they have suggestions to improve? In a recent Kuali webinar, Dr. Karl Kapp, Instructional Technology Professor at Bloomsburg University, touched on process mapping. You can read the summary here.
5. Implement the process. After you’ve done all the brainstorming and analyzing, bring your process to life. A process automation tool can make it easy.
Kuali Build is a no-code process automation tool that includes drag-and-drop workflow visualization. You can essentially take your process map and paste it into Build, then add convenient steps like automatic, customized email notifications or a boomerang which repeats a step if not completed by a certain date.
Process mapping is a great way to improve on the process you have in place. Take the next step in upgrading efficiency with process automation. Using a process automation tool, like Kuali Build, you could slash weeks off of your processes. Check out the Higher Ed’s Guide to eForms and Workflow Automation today to learn more.